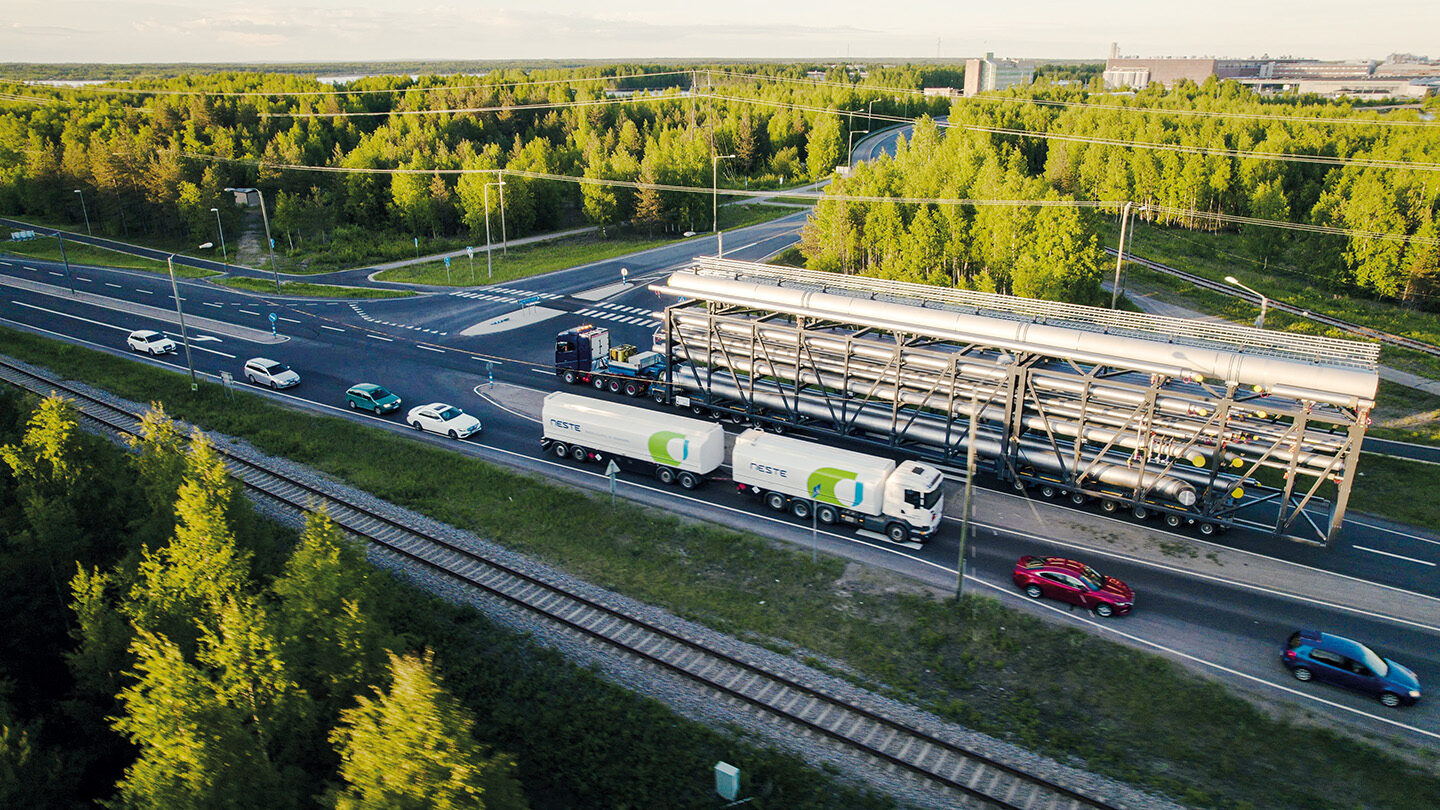
Leading process industry supplier Fineweld is delivering bigger projects than ever
In the last 30 years, Fineweld has become the leading Nordic supplier for large scale process industry investment projects. During that time, the company has taken part in several industrial construction projects in multiple industries, such as battery, chemical, pulp, and mining.
In 2020, Fineweld was chosen as the key supplier for the Swedish battery developer and manufacturer Northvolt’s new cathode material plant. The company did not only have its history’s biggest project ahead, but also the first project that would be carried out in alliance with other suppliers.
“While, for example, engineering and electrification were taken care of by Sweco and ABB, we at Fineweld were in charge of mechanical plant construction – over 50 kilometres of piping, over 2,000 tonnes of steel structures, and equipment installation, to be more specific. Although projects with multiple suppliers are common in the process industry, projects where suppliers work in very close cooperation are not. The alliance contracting model is also quite rare in big projects like this”, says Daniel Sundqvist, CEO.
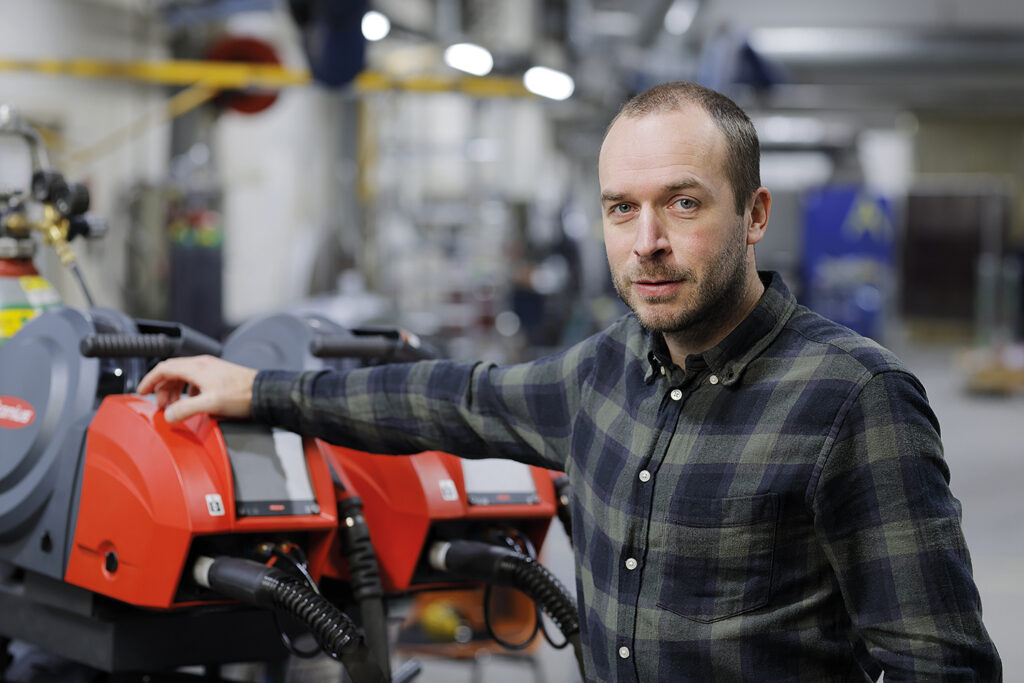
According to Sundqvıst, the alliance model has multiple benefits compared to traditional contracts.
“In the alliance model, the contractors work in continuous cooperation with each other – starting from engineering – and with the client. Managing the project is therefore easier and more efficient for the client.”
When it comes to the battery industry, the manufacturing processes are constantly developing as new innovations are created. This requires a lot of flexibility from the suppliers as well.
“For example, the battery materials utilised in the manufacturing process are quickly changing as better batteries are invented. This is why the alliance contracting is the best decision when building a battery manufacturing plant, for example – close cooperation with other suppliers makes it possible to react to industry changes quickly.”
A year after the cathode material plant project began in Skellefteå in Sweden, Fineweld’s history’s second largest project started in Finland, when Metsä Group selected the company as the key supplier for its new bioproduct mill in Kemi.
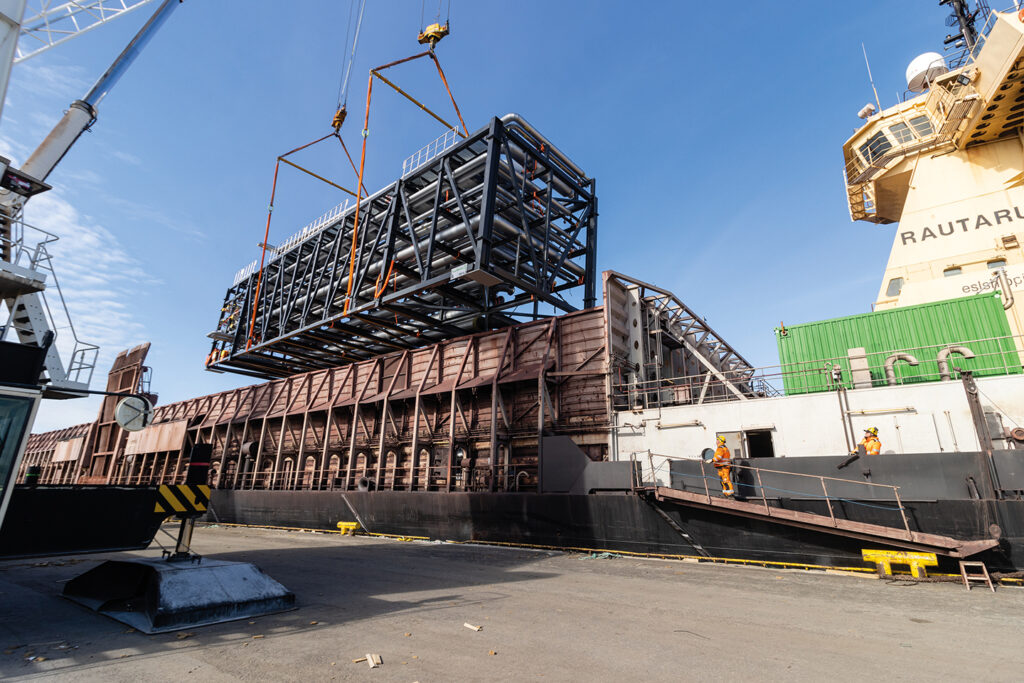
“Our role is to supply all the modular pipe bridges for the mill – this means almost 5,000 tonnes and 60 kilometres of pipe in total. Both this and the project in Skellefteå have lasted for about two years”, states Sundqvist.
Fineweld’s pioneering modular pipe bridge concept has been of great interest to major forestry industry companies when they have planned their billion-euro investment projects. The bioproduct mill project was the third large pipe bridge project for Fineweld in a rather short time.
“We build the pipe bridges almost completely in our own workshops in Kokkola and Kalajoki. This way, less workers are needed in the actual construction site in Kemi, making the process faster and easier to manage on the site.”
However, this semi-modular construction concept is utilised more or less in all Fineweld’s projects, including the cathode material plant project.
“On top of saving money and increasing efficiency, the concept also reduces material waste”, notes Sundqvist.
Building modules almost to completion in Fineweld’s workshops means lifting, installing, and shipping very large units. The biggest unit the company has ever shipped is – for now – a 35 metre long, 8.5 metre wide, and 12 metre high pipe truss bridge that weighed about 160 tonnes. It was delivered to the new bioproduct mill site. Despite handling such heavy units, Fineweld has received recognition for its high level work safety.
“In September 2022, Metsä Group awarded us the Safety Star recognition for our systematic safety work on the bioproduct mill construction site. Although we strive for creating new concepts that increase our effectiveness, safety always comes first for us.”